Troubleshooting Your Equipment: When to Call for Packaging Machine Repair
Troubleshooting Your Equipment: When to Call for Packaging Machine Repair
Blog Article
The Ultimate Overview to Packaging Equipment Repair: Keep Your Workflow Running Efficiently
Comprehending the complexities of packaging maker repair work is critical for maintaining optimum efficiency and lessening interruptions. Routine maintenance not only prolongs the life of these makers yet also addresses common concerns that can hamper efficiency.
Relevance of Routine Maintenance
Regular upkeep of product packaging machines is vital for making sure optimal performance and longevity. By applying an organized upkeep schedule, drivers can identify prospective concerns before they intensify into significant issues. This aggressive strategy not just minimizes downtime yet also extends the life expectancy of the equipment, ultimately resulting in minimized operational expenses.
Routine evaluations permit for the assessment of vital elements such as seals, belts, and sensing units. Dealing with wear and tear immediately protects against unforeseen failures that could interrupt manufacturing and bring about costly repairs. Furthermore, regular upkeep helps guarantee compliance with industry standards and laws, cultivating a secure working setting.
Furthermore, maintenance activities such as calibration, lubrication, and cleaning considerably improve machine performance. Enhanced efficiency equates to consistent item high quality, which is essential for keeping customer complete satisfaction and brand name track record. A well-kept product packaging device operates at optimum rates and lowers material waste, adding to total performance.
Common Packaging Device Problems
Product packaging machines, like any complex machinery, can run into a range of typical problems that may prevent their performance and efficiency - packaging machine repair. One common issue is irregular sealing, which can bring about product perishing and wastefulness if bundles are not effectively sealed. This often arises from misaligned components or worn sealing elements
An additional constant problem is mechanical jams, which can happen as a result of international items, used components, or improper placement. Jams can create hold-ups in manufacturing and rise downtime, inevitably influencing general performance. Furthermore, digital breakdowns, such as failure in sensors or control systems, can lead and interrupt operations to incorrect dimensions or erratic device habits.
Additionally, issues with product feed can also arise, where items might not be delivered to the packaging area continually, causing disruptions. Finally, wear and tear on rollers and belts can result in suboptimal performance, calling for prompt focus to avoid more damage.
Recognizing these common problems is essential for maintaining the stability of product packaging procedures, guaranteeing that equipment runs efficiently and successfully, which in turn assists in conference production targets and maintaining product high quality.
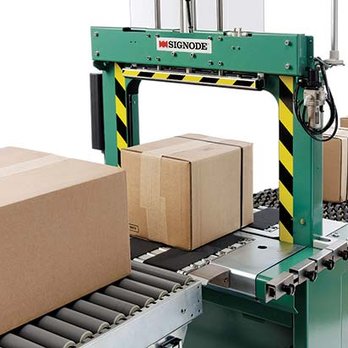
Repairing Methods
Effective repairing methods are important for promptly resolving problems that arise with product packaging devices. An organized technique is vital for recognizing the origin of breakdowns and lessening downtime. Begin by collecting info about the signs and symptoms observed; this may consist of unusual sounds, operational delays, or mistake codes shown on the equipment's interface.
Following, refer to the maker's manual for fixing standards particular to the version concerned. This source can provide useful understandings into typical concerns and recommended analysis actions. Utilize visual examinations to look for loosened connections, worn belts, or misaligned parts, as these physical factors commonly add to operational failures.
Apply a procedure of elimination by testing private equipment functions. If a seal is not creating appropriately, assess the sealing mechanism and temperature settings to figure out if they fulfill functional requirements. Document each step taken and the results observed, as this can aid in future troubleshooting efforts.
Repair work vs. Replacement Decisions
When confronted with devices malfunctions, choosing whether to change a packaging or repair machine can be a complex and critical selection. This choice depends upon a number of key factors, consisting of the age of the maker, the degree of the damage, and the projected effect on operational efficiency.
To start with, click now think about the machine's age. Older makers may need even more regular fixings, leading to higher collective costs that can exceed the investment in a new device.
Operational downtime is one more crucial factor to consider. If fixing the device will certainly cause this contact form extended hold-ups, investing in a new equipment that offers improved performance and reliability could be extra prudent. Think about the schedule of components; if substitute parts are tough to come by, it might be extra calculated to replace the maker totally.
Inevitably, executing a cost-benefit evaluation that consists of both long-term and immediate implications will aid in making an informed decision that aligns with your operational objectives and financial restraints. (packaging machine repair)
Precautionary Steps for Durability
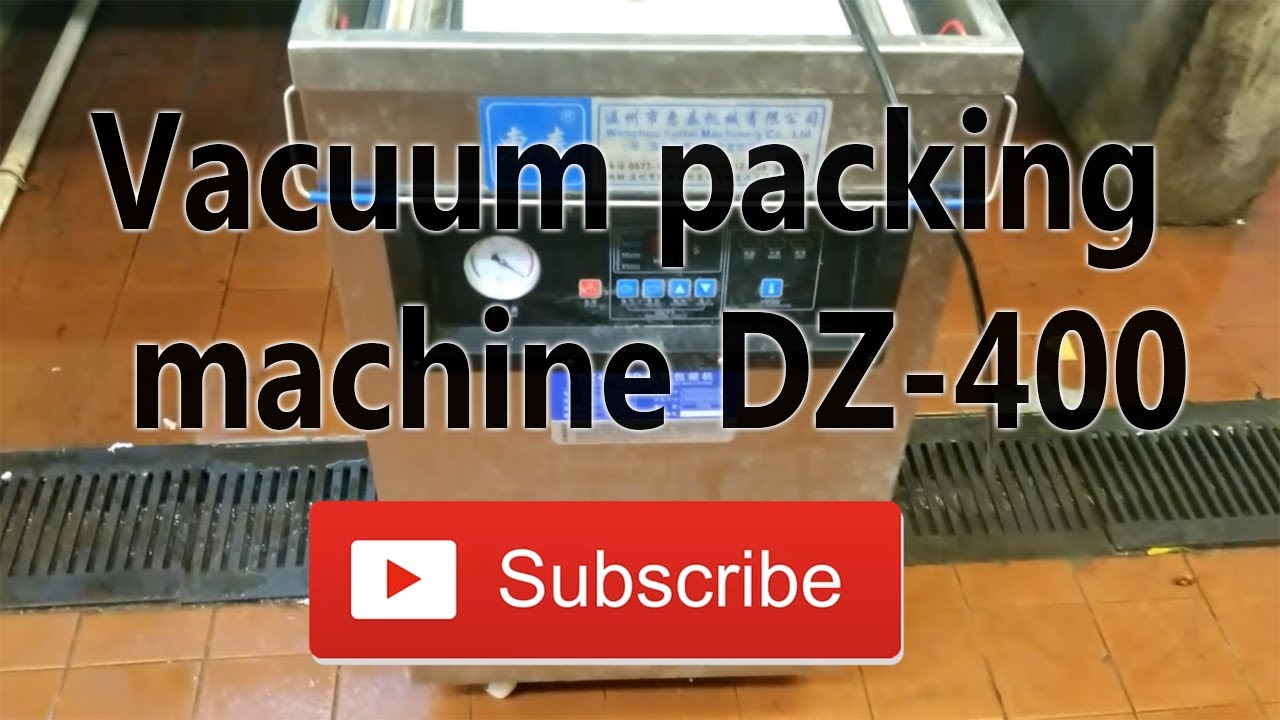
Key safety nets consist of regular lubrication of relocating components, alignment checks, and calibration of sensors and controls. Establishing a cleaning routine to eliminate debris and pollutants from equipment can dramatically lower damage (packaging machine repair). Additionally, monitoring operational parameters such as temperature and vibration can help detect irregularities early on
Training staff to recognize indicators of wear or breakdown is an additional critical part of preventative upkeep. Equipping operators with the knowledge to perform basic troubleshooting can bring about quicker resolutions and decrease functional disruptions.
Paperwork of maintenance tasks, consisting of solution records and inspection searchings for, cultivates responsibility and helps with informed decision-making regarding substitutes and repair services. By prioritizing preventative actions, services can ensure their product packaging makers operate at peak efficiency, eventually resulting in increased performance and decreased functional expenses.
Conclusion
In verdict, the efficient repair and maintenance of packaging equipments are vital for sustaining functional efficiency. Normal maintenance minimizes the risk of usual issues, such as irregular sealing and mechanical jams, while organized troubleshooting techniques assist in prompt resolution of breakdowns. Cautious factor to consider of repair versus substitute choices contributes to economical monitoring of resources. By carrying out safety nets, organizations can enhance maker long life and ensure undisturbed performance in packaging operations.
Comprehending the ins and outs of product packaging equipment fixing is crucial for maintaining optimal performance and minimizing disruptions.Regular maintenance of packaging machines is essential for guaranteeing ideal performance and longevity.Packaging machines, like any kind of intricate equipment, can encounter a variety of common concerns that might impede their performance and effectiveness. If repairing the machine will certainly create extended delays, investing in a brand-new equipment that uses improved effectiveness and reliability could be extra sensible.In conclusion, the effective upkeep click here for more info and repair service of packaging machines are extremely important for maintaining operational effectiveness.
Report this page